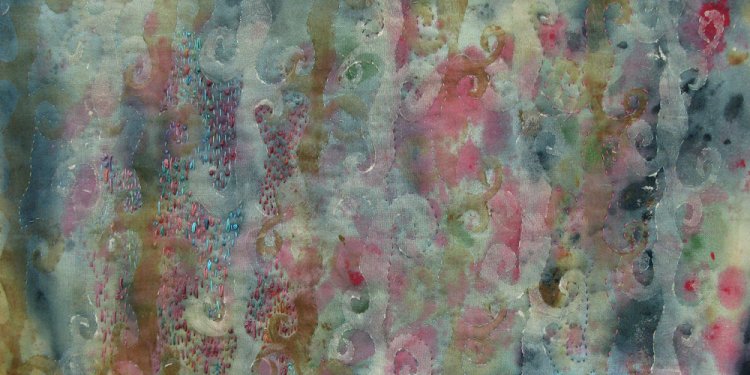
Digitally Printed fabrics
Teresa Coates of crinkledreams.com and Fabric Depot showed us How to Sew Professional-Looking Pillows and brought us a hard-hitting Sewing Needle Comparison. Here she fills you in on Digital Printing on Fabric– the pros, cons and who is making this fabric right now!
Teresa Coates picked up needle and thread as a child and hasn’t stopped sewing since. Her quilting and sewing patterns have appeared in Quilty, Generation Q, Stitch, American Quilt Retailer and Quiltmaker’s 100 Blocks magazines, as well as for Fabric Depot, Robert Kaufman Fabrics and Luke Haynes. She is the social media maven and sewing instructor at Fabric Depot in Portland, Oregon. Follow her sewing adventures at crinkledreams.com and on Instagram.
The first time I heard about digital printing on fabric was five years ago with Spoonflower prints. In the years since, many of the fabric manufacturers have tried their hand at digital printing, with mixed results. Red Rooster, Hoffman California, Elizabeth’s Studio, Robert Kaufman Fabrics and Benartex have all produced digitally-printed fabrics over the past few years, but only a handful have continued on a regular basis. As with any specialized fabric, there are pros and cons.What’s So Great About Digitally Printed Fabrics?
Prints are typically screenprinted onto quilting cotton using a different screen for each color. This process requires careful registration and limits the number of colors that can be used to 16-20, depending on manufacturer.
Digital prints, on the other hand, can have as many colors as there are dyes. It’s potentially limitless. A design could easily be made with 30, 50 or 100 different colors and it would not affect the ability to print the design. Unlike screen printing, resolution is perfect every time and you’ll never get the halo that often occurs when two screen printed, complementary colors bump into each other. Digital printing also eliminates the need for cleaning screens and rinsing out inks giving an environmental benefit.
Without the need for screens, it also makes it possible to increase the length between repeats or even completely do away with them. You could actually print a 10-yard-long design that never repeated. This gives tremendous flexibility to the original artwork and allows for panoramic and/or photographic prints.
The breadth of color choices and design opportunities is what draws the large manufacturers to digital printing. For companies such as Spoonflower and Modern Yardage, it’s the ability to turn around a custom design quickly and easily in very limited quantities.
What’s Not to Love?
The most common complaints about digitally printed fabric have been the cost and the color. Because of the specialized nature of digital printing, including base cloth preparation, limited runs, dyes and machines, the cost per yard for the manufacturer is higher than traditional screen printing. This cost, naturally, gets passed on to the consumer and digital prints are typically a few dollars more per yard. The more limited the run, the higher the cost. Hoffman California generally prints a few thousand yards of each design, whereas Spoonflower prints designs as they are ordered.
Talking with fellow sewists, the biggest complaint has been about color: lack of saturation and fading with both time and sun. This was a problem strictly with the quick turnaround fabrics. Many sewists I questioned complained that the blacks weren’t black enough and other colors were not as bright. Colors faded on fold lines. Each time the fabrics went through the wash cycle, they lost color. This seems to be an issue only for the small printing houses, but one that many sewists accept as the price of having custom fabric made.
The process is different for major manufacturers and the intensity of color is a selling point. Personally, I have used prints from both Hoffman California (Trapezium) and Robert Kaufman Fabrics (Bloominescent). Both were vibrantly saturated off the bolt and remained that way, even after several washes.
The hand of digitally printed fabrics can be slightly odd at first, but wash up beautifully and have a much better drape and feel after the first wash. Hawthorne Threads and Hoffman both agree that washing the fabric before using it will give you better results.
Who Is Making It Now?
Hoffman California has several lines available in quilt shops this year including Ridge Rock, Poinsettia, Trapezium, and Skylines. These are coordinated to go with their 1895 batik blender collection. Elizabeth’s Studio has the Digital Garden coming to stores in August. Hawthorne Threads has more than a dozen collections that are designed and digitally printed in-house, including Calypso, Fawn, Coyote and Zambezi.