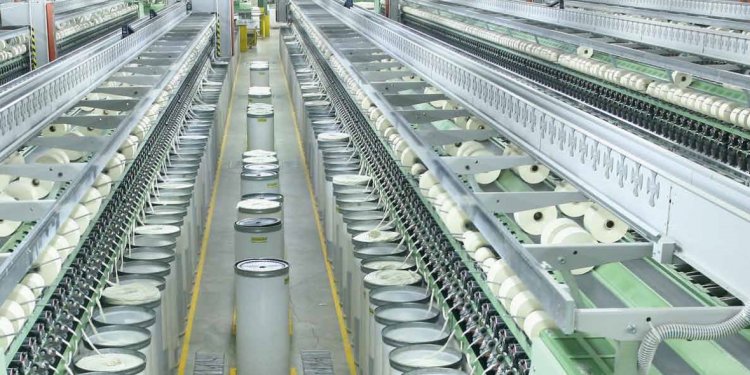
Textile yarn manufacturing process
Yarn and Yarn Manufacturing:
An assemblage of fibers that is twisted or laid together so as to form a continuous strand that can be made into a textile fabric. So a yarn is a strand of natural or man made fibres or filaments that have been twisted or grouped together for use in weaving, knitting, or other methods of constructing textile fabrics. The type of yarn to be manufactured will depend on the fibres selected;the texture, or hand, of the fabric to be made; and qualities such as warmth, resiliency, softness, and durability required in the fabric's end uses.
Yarn Manufacturing Process
Input - output and objects of individual section of yarn manufacturing (for cotton):Input-output and objects of individual section of yarn manufacturing for Cotton is given below step by step-
01. Section: Mixing of raw cotton.
Input:
Bale of raw cotton.
Object:
- To mix different staple fibres properly.
- To minimize cost.
- To produce better quality of yarn at last stage(ring).
Mixed raw cotton.
02. Section: Blow room
Input:
Mixed raw cotton.
- To open the fibres.
- To remove the trush.
- To mix the fibers.
- To make uniform lap sheet.
Lap.
03. Section: Carding.
Input:
Lap.
- To remove fine trush.
- To remove short fibres, neps, motes and foreign materials too.
- To produce regular sliver.
Carded Sliver.
04. Section: Draw frame
Input:
Sliver.
- To parallel the fibres.
- To blend and mix the fibres.
- To reduce weight per unit length.
- To make uniform sliver.
Regular sliver.
05. Section: Lap former.
Input:
Regular sliver.
- Forming the interfacing or lap, which is employed to feed the combing machine.
Lap.
06. Section: Combing.
Input:Lap.
- To remove short fibres.
- To remove fine trash and dirt.
- To parallel and straight the fibres.
Regular/combed sliver.
07. Section: Drawing (Finisher)
Input:Regular/combed sliver.
- To parallelize the fibres.
Uniform sliver/drawn sliver.
08. Section: Simplex.
Input:Uniform sliver/drawn sliver.
- Draft the material.
- Insert a small amount of twist.
- To make bobbin with roving of conical shape.
Roving.
09. Section: Ring.
Input:Roving.
- Drafting (attenuation).
- Insertion of twist for strengthen the yarn.
- To wind the yarn on to the ring tube/bobbin.
Yarn.
10. Section: Cone winding.
Input:Yarn.
- To transfer the yarn from ring cop/tube. To a large package(weight:2-2.5 lbs)
- To remove the faults present in the yarn.
- To get better quality of yarn.
Yarn on cone.
11. Section: Reeling.
Input:Yarn on cone.
- To clean the slubs.
- To make hanks(1680) each.
Hanks.
12. Section: Bundling.
Input:Hanks.
- To make Bundle.
Bundle of 10 lbs.
13. Section: Baling.
Input:Bundle.
- To make a bale for marketing.
Bale of 400 lbs.
Conclusion:
Completing this process we can, get yarn and use it different work. This process only use for cotton yarn(carded/combed) manufacturing.