Silk Screen Printing
A Brief History
Silk screen printing originated in Japan, evolving from the traditional art of stencil printing on fabric.
Cutting intricate patterns was a highly prized skill in Japan, but it was hindered by the inherent fragility of paper stencils, and their tendency to tear during handling and printing.
The problem was solved by gluing strands of silk (or human hair) to the stencil to increase its strength and durability.
New levels of intricacy were achieved using this technique, and stencils became covered with an ever-expanding mesh of supporting threads.
stencil with silk threads
The next logical step was to stretch a piece of woven silk on a wooden frame and then glue the stencil directly onto the silk mesh: the first "silk screen."
The art of silk screen printing moved to the West in the early 20th century, first as a commercial printing method, and then as a fine art form: serigraphy. It was adapted by the wallpaper industry as a method for making the highest quality handprints.
Our Studio
We print all of our papers at our Benicia, California factory.
Please note that our facility is no longer open to the public.
Printing Tables are 90 feet long and each holds 6 rolls of wallpaper. Metal rails along the side of the table have adjustable knobs which are set to the particular repeat of the pattern to be printed. A complex pattern for an average size Victorian room can require over 1, 000 individual impressions.
Artwork: Many of our patterns have been created by hand in the traditional manner by painting on acetate or cutting a stencil using a graphic arts film (as shown here). For every pattern we create, a separate stencil must be prepared for each different color, and all must align perfectly.
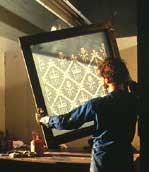
Screen Making is done by coating a silk screen with a photo-sensitive emulsion, essentially creating a large piece of film. The screen and artwork are sandwiched in a large vacuum frame and exposed to light. Areas exposed to the light become impervious; the other areas can be washed out. In the early days we used silk on a wooden frame; today it's monofilament polyester on a titanium frame.
Paint is forced through the stencil using a plastic-bladed squeegee. The printer must skip every other repeat to prevent the silk screen frame from falling in wet ink. Each screen lays down one color - if a pattern has eight colors it must be printed eight times with eight different screens.
Source: www.bradbury.com