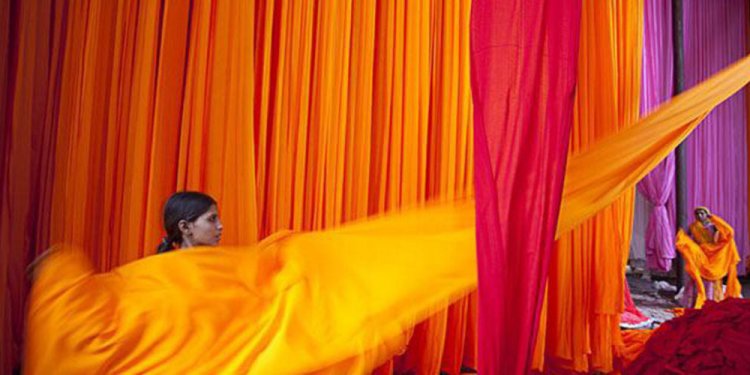
Printing process in textile industry
The Dyes used for printing mostly include vat, reactive, naphthol and disperse colours which have good fastness properties. The pigments, which are not truly dyes, are also used extensively for printing. These colours are fixed to the fiber through resins that are very resistant to laundering or drycleaning. Pigments are among the fastest known colours and are effective for light to medium shades. If used for applying dark colours, they may crock or rub off. Improved resins, better pigments or more effective anticrock agents must be used to solve this problem. Cheap prints are made from basic colours mixed with tartar emetic and tannic acid but they are not acceptable in todays market.
For cotton printing vat and reactive dyes are generally used. Silk is usually printed with acid colours. Wool is printed with acid or chrome dyes but before printing it is treated with chlorine to make it more receptive to colours. Manmade fibers are generally printed with disperse and cationic dyes.
Methods of Printing
Three different approaches or techniques are prevalent for printing colour on a fabric: Direct, Discharge and Resist
Direct Printing
It is the most common approach to apply a colour pattern on fabric. It can be done on white or a coloured fabric. If done on coloured fabric, it is known as overprinting. The desired pattern is produced by imprinting dye on the fabric in a paste form. To prepare the print paste, a thickening agent is added to a limited amount of water and dye is dissolved in it. Earlier corn starch was preferred as a thickening agent for cotton printing. Nowadays gums or alginates derived from seaweed are preferred because they are easier to wash out, do not themselves absorb any colour and allow better penetration of colour. Most pigment printing is done without thickeners as the mixing up of resins, solvents and water itself produces thickening.
Discharge Printing
In this approach, the fabric is dyed in piece and then it is printed with a chemical that destroys the colour in the designed areas. Sometimes, the base colour is removed and another colour is printed in its place. The printed fabric is steamed and then thoroughly washed. This approach is on decline these days.
Resist Printing
In this technique, a resist paste is imprinted on the fabric and then it is dyed. The dye affects only those parts that are not covered by the resist paste. After dyeing, the resist paste is removed leaving a pattern on a dark background.
There are various methods of printing in which one of the above three techniques is used - Block Printing, Roller Printing, Duplex Printing, Stencil Printing, Screen Printing, Transfer Printing, Blotch Printing, Jet Spray Printing, Electrostatic Printing, Photo Printing, Differential Printing, Warp Printing, Batik Dyeing, Tie Dyeing, Airbrush (Spray) Painting and Digital printing
Block Printing
The designs are carved on a wooden or metal block and the paste dyestuff is applied to the design on the face of the block. The block is pressed down firmly by hand on the surface of the fabric.
Roller Printing
In this machine counterpart of block printing, engraved copper cylinders or rollers are used in place of handcarved blocks. With each revolution of the roller, a repeat of the design is printed. The printed cloth is passed into a drying and then a steam chamber where the moisture and heat sets the dye.
Duplex Printing
Printing is done on both sides of the fabric either through roller printing machine in two operations or a duplex printing machine in a single operation.
Screen Printing
It is done either with flat or cylindrical screens made of silk threads, nylon, polyester, vinyon or metal. The printing paste or dye is poured on the screen and forced through its unblocked areas onto the fabric. Based on the type of the screen used, it is known as 'Flat Screen Printing' or 'Rotary Screen Printing'.