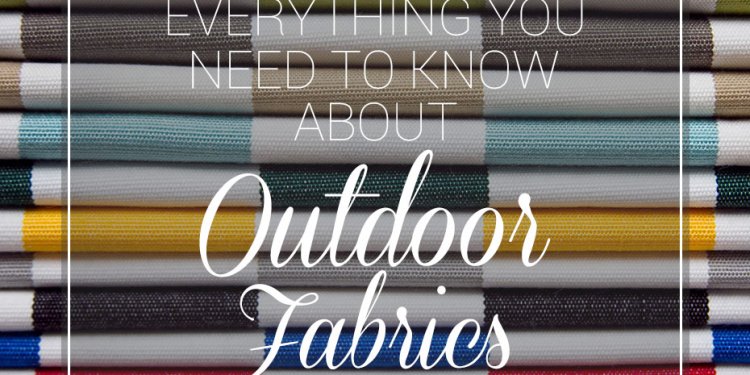
Yarn making process
The present activities of the company involve processes that go into producing quality yarn. The best quality raw cotton is processed in state-of-the-art machineries using the latest technical know-how, to produce the finest quality yarn.
To get an uniform end product consistently from highly variable characteristics of input fibres, mixing of different lots is done.
Blow room consists state of art machines that carry out Opening, Cleaning, thorough Mixing and decreasing the tuft size smaller and smaller, to feed material to Carding uniformly and continuously. Blow Room line is equipped with world class technology cotton contamination sorter like JOSSI.
"Card is the heart of the spinning mill" and "Well carded is half spun" are two proverbs of the experts. The purpose of Carding is to open tufts to individual fibres, neps reduction, elimination of dust and orientation of fibres into sliver form. In Our Installation we are having a flexibility to run different processes.
The object of draw frame is to double and draft the slivers and thereby make even sliver and parallelization of fibres i.e. hooks created at Carding are removed. Our Machines are equipped with 1000mm cans to avoid no.of joints which directly effects quality of final yarn.
The object of Lap Former is preparation of Lap from slivers with optimum parallelized fibres and feeding of trailing hooks from Carding as leading hooks at Comber to reduce long fibre loss in the noil.
Combing is the process which is used to upgrade the raw material and to produce an improvement in yarn quality by elimination of short fibres, elimination of remaining impurities and elimination of neps.
The object of Fr. draw frame is to double and draft the slivers and thereby make even sliver, parallelization of fibres and auto leveling of linear density variations in feeding to get constant linear density of output sliver.
The object of Simplex is to produce roving suitable to feed Ring frame by means of attenuation - drafting of sliver, twisting the drafted strand and winding the twisted roving on a bobbin. Our machinery is equipped with automatic tension controls to produce better quality of roving in order to get best quality of yarn.