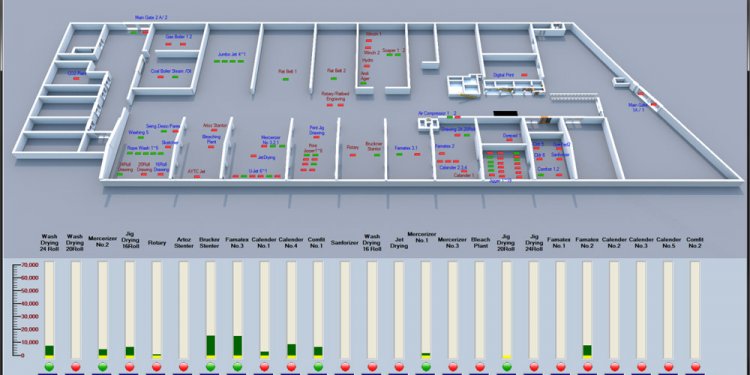
Textile Printing Industries
Lisagor’s method of 3D printing onto mesh fabric started with a combination of her experiences. “I was working on a wrist fracture brace project, which was printed nylon, and I just wanted to incorporate a soft material with that, ” Lisagor told me. “So, that, combined with some other experiments and 3D printing textile-like things, led me to see where printing onto textiles would go.” The process begins by printing out the ‘plate’ layer first (using PLA filament), which acts as a foundation for the fabric and textile design to connect. Depending on the shape of the textile print, the appropriately printed PLA ’plate’ is created on the Cube 3’s print surface.
After 3D Systems’ newly enhanced software halts the project once the plate is printed, the specialty mesh fabric is carefully laid and lightly glued down across it. The mesh fabric is then placed on top of the plate, the Cube 3 continues onto the bigger part of the project, this time printing the textile through the mesh and onto the plate layer, creating (for lack of a better term) a “fabric sandwich”.
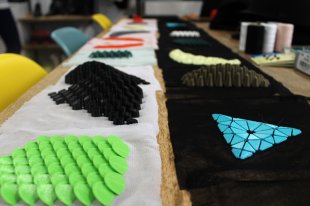
With Fabricate’s official release, today, however, the fabric sandwich has been improved a bit. From the tutorial above, you’ll see that the process now begins with glue, followed by the fabric, followed by the 3D printed .textile, a new 3D file format specifically made for the new platform.
At the end of her presentation, Lisagor had presented us with dozens of different textile-on-mesh designs for us to sample and sew onto clothing ourselves. The textile to mesh fabric to clothing is just the first step for Lisagor, who eventually hopes to print her designs directly onto a variety of fabrics, rather then having to use fabrics like mesh as a middle man. 3D Systems’ more professionally-styled printers, such as the CubePro or the ProJet Series, do have the potential for more grandiose textile designs compared to the Cube 3.
But the point of Lisagor’s project is to bring these textile designs and ideas into our homes, seemingly trying to prove that professional and DIY designers aren’t that exclusive from one another after all. Lisagor’s future goals with textiles involves using the 3D Systems’ printer to combine different types of their exclusive filaments together. “The cartridge system has some really great embedded advantages and I think in the upcoming projects you’ll see that even more, ” she explains. “You’ll see that you can combine two different printing materials together beyond the fabric at home with desktop printing.”
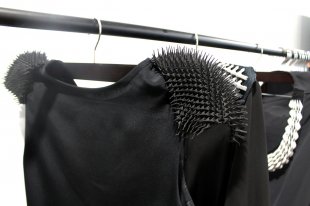
3D Systems and Lisagor certainly see a place for 3D printing in the fashion design world, but instead of aiming straight for the top of the fashion food chain, she wants this extension of fashion to start at the homes of the more thrifty, DIY enthusiasts. And, now, upon today’s official release of Fabricate, those interested can begin implementing the platform at home or in their own studios. On the Fabricate site, there are three .textile patterns, but 3D Systems plans to release more on a monthly basis, along with compelling collaborations with fashion designers to demonstrate the technology’s possibilities.
Fabricate packs can be purchased on the 3D Systems site, with a $149 Fabricate Design Pack buying designers a filament cartridge, textile squares, and six Fabricate .textile designs; however, a Fabricate Starter Pack comes with a Cube 3D printer, cartridges, textile squares, and a set of six .textile designs for $1, 199. This is just the start of the Cube 3’s venture into the fashion world, but with Lisagor leading the way, 3D Systems may even find their 3D printed influence both in the home and on the runway in the near future.